In Australia’s pharmaceutical and biotechnology industries, GMP (Good Manufacturing Practice) clean rooms have high requirements for environmental cleanliness, temperature and humidity control and logistical efficiency, and GMP cleanroom workshop speed doors, with their high sealing, fast opening and closing functions, have become the ideal solution for GMP clean rooms, helping companies to meet stringent quality and safety standards. In this article, we will discuss in detail the features, technical advantages, application scenarios and purchase guidelines of GMP clean room workshop speed door.
What is GMP Clean room Workshop Rapid Door?
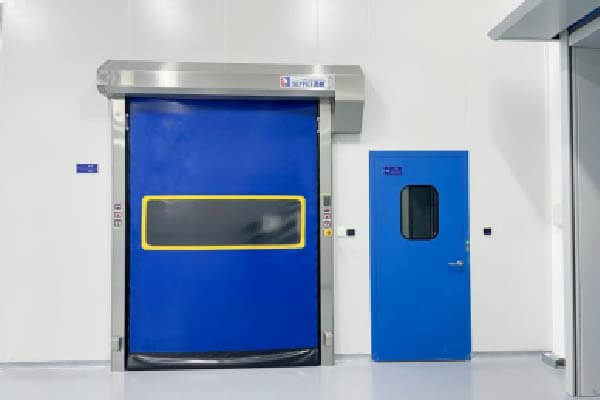
GMP Cleanroom Workshop Speed Doors is a kind of industrial door designed for high clean environment with fast, high sealing and automation. Its main functions include:
High sealing: effectively prevent outside air, dust and microorganisms from entering the clean room, and safeguard the clean environment.
High opening and closing speed: usually the opening and closing speed can reach more than 1.5 meters/second, ensuring efficient flow of logistics.
Automation control: Equipped with intelligent system, it can automatically control the opening and closing of the door, reducing human error in operation.
The Unique Needs of a GMP Cleanroom Environment
In a GMP clean room, strict air cleanliness and temperature and humidity control is the basis for maintaining compliance in the production environment. Particularly in pharmaceutical and food processing lines. Any contaminants entering the production line can negatively impact product quality and even lead to the scrapping of an entire batch. The demand for controlled air flow in GMP environments has made speed gates a centerpiece of cleanliness assurance. The high speed opening and closing function reduces the air convection time and provides technical support to maintain a specific level of cleanliness.
Reasons why GMP cleanroom workshops need fast doors
In the GMP clean room in the strict production environment. The use of fast doors is critical, especially in the pharmaceutical, food processing, medical device manufacturing and other industries. GMP standards for the cleanliness of the workshop, environmental control and the standardization of the operation process put forward stringent requirements, any possible sources of contamination need to be Any possible source of contamination needs to be isolated and controlled. The high sealing, automation, high opening and closing speeds and low maintenance characteristics of fast doors make them an important part of GMP-compliant clean rooms.
1. Core assurance of cleanliness control
Air cleanliness in a GMP cleanroom is critical to the manufacturing process because airborne particles or contaminants. Once introduced into the production line, may affect the safety and efficacy of the product. The sealed design of a speed door effectively prevents outside dust, microorganisms and other contaminants from entering the shop floor by reducing air flow. High-quality speed doors are generally double-sealed or magnetically sealed to ensure a strong barrier every time the door is closed.
2. Efficient temperature and humidity management
GMP cleanrooms often need to operate in a specific temperature and humidity environment. For example, active ingredients in the pharmaceutical industry need to be stored and processed at a certain temperature to prevent deterioration or degradation. Rapid doors can reduce the frequency of indoor and outdoor air exchange and maintain a stable temperature and humidity environment. Helping to avoid product quality problems caused by temperature and humidity fluctuations. In addition, the heat preservation performance of the fast door is more significant in low-temperature clean rooms or refrigerated rooms. Which can effectively save energy consumption and reduce the operating costs of enterprises.
3. Reduce the possibility of cross-contamination
In multi-production line or multi-area parallel GMP workshop, the contamination isolation between different clean zones is crucial. Rapid door in the clean area between the partition function can not only effectively separate the air. But also in the shortest possible time to complete the opening and closing, in order to reduce the possibility of cross-contamination. For example, in the pharmaceutical production process, the production area that needs to maintain aseptic environment. Through the high sealing and self-repairing function of the rapid door, can avoid the environmental exposure and contamination risk brought about by frequent opening and closing.
4. Enhance the efficiency of logistics operations to ensure smooth flow of processes
GMP workshop usually requires efficient logistics in and out. Such as raw materials, semi-finished products, finished products in and out, equipment and personnel circulation. The high-speed opening and closing (usually up to 1-2 seconds) of the fast door greatly shortens the operation waiting time, helping enterprises to meet the cleanliness standards while realizing smooth logistics management. In addition, the automation control system of the rapid door can be combined with the intelligent system of the workshop. For example, through the radar sensor, infrared sensor and other functions. So that the door body will open automatically when the personnel or equipment is close to it, to reduce the manual operation and improve the efficiency.
High speed doors in GMP cleanroom application scenarios
Separation of production area and clean area
In GMP production workshops, high speed doors are used to separate areas with different cleanliness levels and reduce cross-contamination. The use of fast doors in key locations such as sterile areas and raw material storage can ensure the flow of materials and personnel without affecting cleanliness.
Equipment entrances for high cleanliness requirements
In pharmaceutical and food processing plants, equipment and raw materials often need to enter and exit clean areas. The high sealing and high speed response of a speed door ensures that no air is exchanged during circulation. Reducing the risk of contamination.
Temperature and humidity controlled zones
In areas with specific requirements for temperature and humidity. Such as refrigerated truck rooms or special temperature-controlled workshops, the insulation function of the speed door can help to maintain a constant environment, effectively saving energy consumption.
Technical parameters and standards of the rapid door
Opening and closing speed: usually in the range of 0.8 to 1.4 meters per second, to ensure efficient workshop logistics.
Sealing grade: It is recommended to choose products with high sealing grade (e.g. IP65).
Material: Durable, anti-static, high sealing material, such as high-strength PVC.
Temperature and humidity applicable range: suitable for different temperature and humidity control areas, from cold storage to clean room.
Practical application examples
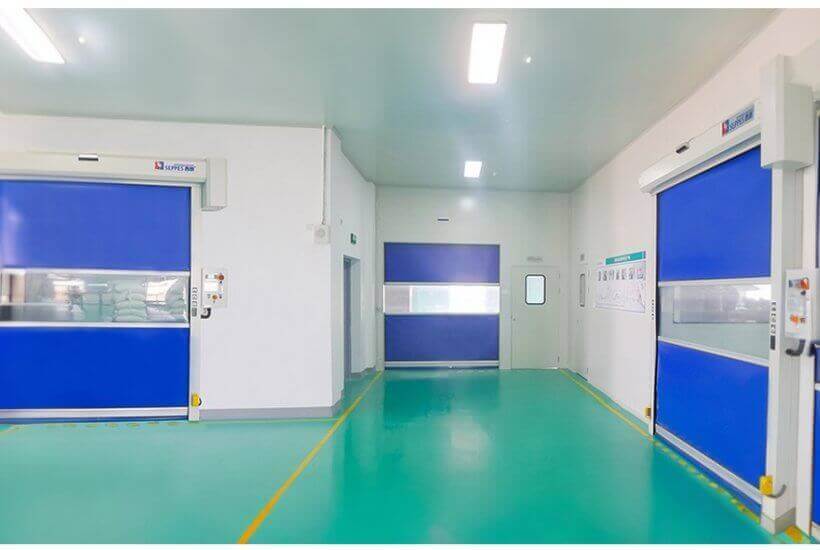
In a well known pharmaceutical company in Australia, SEPPES speed doors are widely used in various areas of its GMP clean room, especially in the separation of production and storage. The company strictly controls the cleanliness, temperature and humidity of each production stage. And SEPPES rapid doors meet the company’s needs by virtue of high sealing, efficient operation and chemical-resistant material design. The system is also equipped with an intelligent sensing system. Which guarantees a contact-free environment in logistics operations and greatly improves the efficiency of cleanliness control.
Future Market Outlook and Technology Development
With the increasing demand for cleanroom doors in the pharmaceutical, medical and food industries, rapid doors will continue to be upgraded and innovated. And future rapid doors will be more intelligent and energy-saving and environmentally friendly. Intelligent systems will lead to easier environmental control and maintenance. While low-energy designs will meet the needs of companies to save energy. In addition, advances in materials will make rapid doors more lightweight and durable, reducing the frequency of equipment maintenance.
FAQ
Q1:What is the main function of GMP cleanroom workshop speed doors?
A: GMP clean room speed door has high sealing and fast opening/closing function. That helps to control the air cleanliness and improve the operation efficiency.
Q2:What factors should be considered when choosing cleanroom speed door?
A: The main focus is on sealing, automation control, chemical resistance and impact resistance to meet the needs of GMP environment.
Q3:What are the common materials used for the fast doors?
A: Mainly high-strength PVC and stainless steel with excellent chemical resistance and abrasion resistance for high cleanliness environment.
Summarize
Speed doors in GMP clean rooms not only provide protection for workshop cleanliness and logistics efficiency. But also help companies realize efficient operations and cost savings. In the future, with the upgrading of the demand for clean environment. The intelligent and energy-saving design of the rapid door will also continue to progress. Making the environmental control of GMP workshop more intelligent and efficient. Choosing high quality fast door equipment is not only the key to guarantee product quality. But also an important decision in line with the market development trend.